Życie maszyn budowlanych nie jest usłane różami. Najgorzej mają się te maszyny, których jest najwięcej, wraz ze wzrostem przepracowanej liczby godzin są warte coraz mniej, a ich obsługa jest coraz bardziej ograniczona, aż w końcu lądują w krzakach w celu zgnicia. Trochę lepiej mają się maszyny duże i bardzo drogie, których resurs jest zależny głównie od poziomu utrzymania na przestrzeni lat. W przypadku każdej jednak maszyny, przychodzi moment kiedy musimy zdecydować czy idziemy w kierunku wysokonakładowej modernizacji, czy też odpuszczamy i pozbywamy się lub złomujemy maszynę, żeby niepotrzebnie nie zasilać zasobów konkurencji.
Silniki maszyn budowlanych, jako ich serce, są szczególnym komponentem. Na przestrzeni 30-40-50lat, technologia budowy silników wysokoprężnych zmieniła się o dobre 3-4 generacje, I pomimo tego, że rynek silników przemysłowych jest długowieczny, to serwisowanie jednostek ,które historycznie pamiętają lata 70te stało się problemem. Główne źródła problemów to na pierwszym miejscu, niechęć serwisów do obsługi starych silników, drugi to ograniczenia w dostępności do części zamiennych, a trzeci to zwiększona awaryjność wynikająca z samego wieku silnika.

Na początku 2023r miałem okazję przeprowadzić modernizację silnika podbijarki torowej Plasser&Theurer 09-32CSM, wyposażonej w silnik Deutz BF12L413F, którego konstrukcja pamięta lata 70te. Silniki Deutza z rodziny 413 zdecydowanie można uznać za bardzo udane. Do dzisiaj pracują w wielu maszynach, a jeszcze kilka lat temu widziałem, jak nowe egzemplarze takich silników były montowane w maszynach górniczych produkowanych u nas na rynki wschodnie. Głównym argumentem za ich użyciem była właśnie niezawodność i dzięki chłodzeniu powietrzem, dobra kompatybilność z zimnym klimatem.

Po co w takim razie wymieniać taką jednostkę na inną? Powodów jest kilka, i każdy broni się bardzo dobrze. Pierwszym jest coś co nazwał bym niechęcią serwisów do obsługi bardzo starych silników. Jako mechanik dobrze to rozumiem, grzebanie w tak starym sprzęcie to zawsze ryzyko, że coś zawiedzie, a klienci nie są skorzy do rozwiązań kompleksowych, które generują wysokie koszty. W efekcie czasami lepiej jest nie wkładać rąk w urządzenia, za którymi idzie ryzyko problemów i niezadowolenia klienta. Drugim problemem jest brak takich jednostek na rynku wtórnym. Oczywiście w skali europy pewnie uda nam się taki silnik znaleźć, ale niemal na pewno będzie to jednostka w stanie do kompletnego remontu, który dla używanej jednostki przeprowadzić trzeba w mniejszym lub większym zakresie zawsze. Szczególnie ze względu na same koszty związane z logistyką jego wymiany w takiej maszynie jak podbijarka torowa. Trzeci powód to bardzo zbliżony koszt zakupu u producenta jednostki fabrycznie regenerowanej starego i nowego typu. W Deutz AG w ramach programu X-change, można nadal zamówić fabrycznie regenerowany silnik typu 413, ale jego koszt jest w zasadzie jednakowy do TCD2015V8, na który padł wybór. W przypadku starego typu silnika, odpadłyby koszty związane z przebudową maszyny, ale nie rozwiązali byśmy problemów wymienionych w pierwszej kolejności. Dodatkowo, analizując dane producenta dotyczące zapotrzebowania obu jednostek na paliwo, prosta kalkulacja wskazała, że jeżeli maszyna będzie pracować, to w ciągu kilku lat inwestycja ma szanse zwrócić się w samych kosztach paliwa. Jest jeszcze za wcześnie, żeby to zweryfikować w praktyce, ale nie ma wątpliwości, że efektywność silników TCD2015 stoi na zupełnie innym, wyższym poziomie.
Z kim współpracować w zakresie dostaw?
Decyzja o wymianie jednostki napędowej na nowszą, zapadła już w 2021r a kompleksowej realizacji zadania podjął się jeden z autoryzowanych serwisów Deutz w Polsce. Cała historia okazała się kompletną klapą i z perspektywy czasu, wiem z całą pewnością, że nie mieli żadnej możliwości wywiązać się z zadania. Serwis ten nie dotrzymał żadnych zadeklarowanych terminów, a kiedy zdecydowaliśmy się zasięgnąć informacji w centrali Deutz na Polskę, firmie BTH Fast, okazało się, że silnik na który czekaliśmy został wbrew zasadom firmy zamówiony przez serwis z innego źródła (niewiadomego). Dodatkowo, nierzetelny serwis postanowił wyrazić swoje niezadowolenie naszą interwencją i usłyszeliśmy, że wtykamy nos w nie swoje sprawy i zerwał umowę w terminie kiedy jej realizacja powinna być na finałowym etapie… Biorąc pod uwagę, że w marcu 2022 roku mieliśmy na na hali rozebraną maszynę bez silnika i nikłe perspektywy na wykonanie modernizacji, jedyną i bolesną decyzją była ta, o poskładaniu maszyny do kupy i odłożeniu całej operacji na kolejny rok. Dalszą współpracę w zakresie dostawy jednostki napędowej, podjęliśmy z głównym przedstawicielem Deutz AG na Polskę, firmą BTH Fast. I tą współpracę bardzo sobie chwalę. Rzetelność, terminowość i wsparcie firmy BTH Fast stoją na bardzo wysokim poziomie.
Dlaczego warto współpracować z autoryzowanym dostawcą Deutz? Musimy pamiętać o tym, że modernizacja, taka jak omawiana to w zasadzie budowanie prototypu, który musi zadziałać od pierwszego razu. Dodatkowo, wszystko musi być zaprojektowane, zaplanowane i przygotowane z dużym wyprzedzeniem. Nie ma możliwości zabudowania wszystkiego od ręki w naturze, chociażby ze względu na to, że czas oczekiwania na niektóre z komponentów to 3-4 miesiące. W takim przypadku współpraca z autoryzowanym dostawcą producenta, ma kluczowe znaczenie. Przede wszystkim w ramach takiej współpracy, mamy możliwość dostępu do wszelkiej dokumentacji technicznej, charakterystyk komponentów, cyfrowych modeli STEP, które są niezastąpione przy projektowaniu instalacji i rzetelnej informacji o dostępności i koszcie komponentów.
Jak wygląda zakup silnika w Deutz AG?
Tutaj sprawa robi się ciekawa. Z początku nie mogłem zrozumieć dlaczego koszt silnika fabrycznie nowego i fabrycznie regenerowanego X-Change różnią się nieznacznie (samego silnika). W praktyce okazało się, że silnika nowego zakupić nie możemy, ponieważ wiąże się to z koniecznością zakupu silnika w specyfikacji odpowiadającej aktualnym normom. Czyli w praktyce, musielibyśmy zakupić jednostkę conajmniej z bardzo drogim układem wydechowym wyposażonym w DPF. Nie było na to ani czasu, ani miejsca (fizycznie w maszynie). Z drugiej strony, zakup silnika z programu X-Change Deutza, też obarczony jest ograniczeniami. Mianowicie, musimy zamówić silnik o określonym numerze seryjnym, w wyprodukowanej wcześniej specyfikacji. Tak, jak zamawia się część zamienną. Tutaj pomoc przedstawiciela Deutz jest niezbędna, ponieważ tylko on ma dostęp do informacji o wyprodukowanych silnikach.
Trzeba szukać kompromisów, szczególnie, że dokupowanie i wymiana podzespołów silnika jest później bardzo kosztowna. I tak, zamiast dwóch mniejszych alternatorów zostajemy z jednym dużym, sprężarkę klimatyzacji musimy gdzieś „dokleić” itd. Kłopotliwe ale do zaakceptowania. Kompletując do silnika sterownik ECU (engine control managment), również musimy dobrze zweryfikować jak dokładnie został zaprogramowany, ponieważ okazuje się, że mimo obecności różnych funkcji w specyfikacji i na schematach ,sterownik który otrzymamy nie będzie w niektóre z nich wyposażony, lub będą one działały nieznacznie inaczej niż się spodziewamy. Doradcy w Deutz, też nie wiedzą absolutnie wszystkiego i kluczowa jest umiejętność zadawania właściwych pytań i we właściwy sposób.

Sam silnik z programu X-Change jest nie do odróżnienia od silnika fabrycznie nowego. Próbowałem znaleźć ślady zastosowania jakiegokolwiek komponentu, który miałby oznaki wcześniejszego użytkowania, ale bez efektu. Jeżeli silnik jest wyposażony w używany blok, wał korbowy i ewentualnie korpusy głowic, to jest to wszystko co łączy go z regeneracją silnika.
Problemy i kwestie techniczne
W przypadku tej konkretnej modernizacji, dwie kwestie stanowiły główne źródła problemu. Pierwszym źródłem problemów było zastąpienie silnika chłodzonego powietrzem, silnikiem chłodzonym cieczą a drugą była konieczność zaprojektowania hydraulicznego napędu wentylatora chłodzącego. Oba problemy łączyły się w jedno główne zagadnienie.
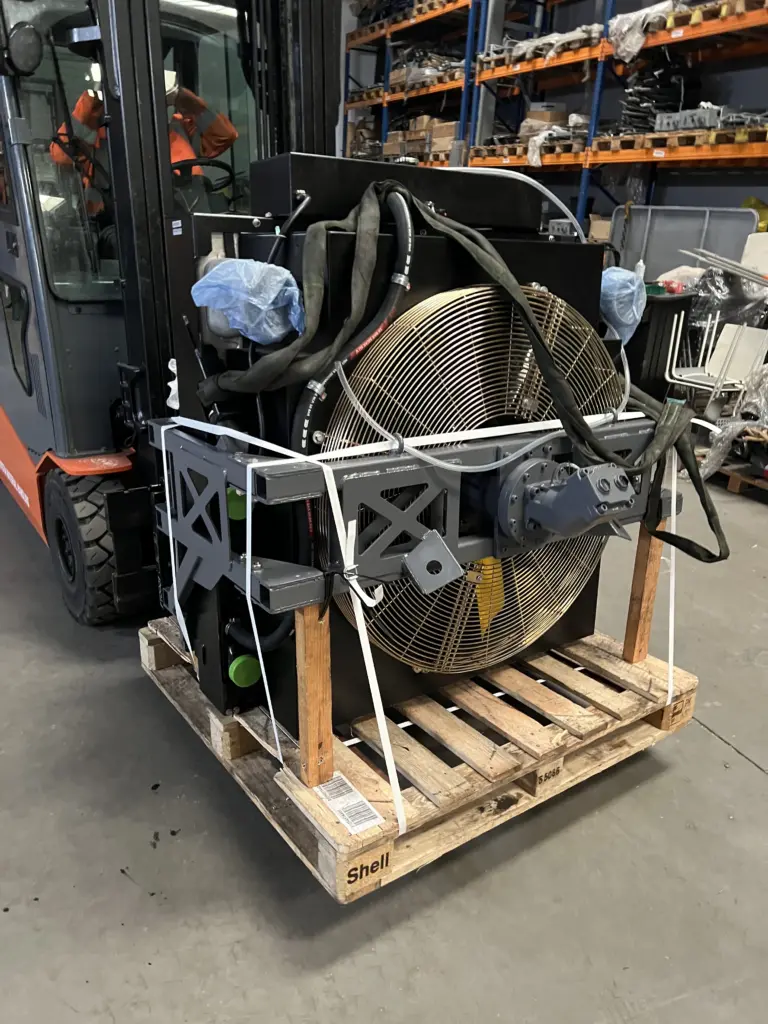
W przypadku podbijarki CSM 09-32, zarówno przód jak i tył wału korbowego, wykorzystywane są do napędu osprzętu maszyny. Tył wału korbowego (strona koła zamachowego), połączony jest wałem napędowym z przekładnią automatyczną ZF, która zapewnia maszynie jazdę transportową. Natomiast przód wału korbowego poprzez wał napędowy, napędza przekładnie pomp hydraulicznych, które zasilają maszynę podczas podbijania toru. Sytuacja w której moc z wału korbowego jest odbierana z obu jego stron stanowi rzadką konfigurację. Najczęściej z przodu silnika mamy zamontowany wentylator chłodnicy, a sama chłodnica zamontowana jest bezpośrednio przed silnikiem i wspiera się na tych samych podłużnicach. Ze względu na konieczność zamontowania chłodnicy silnika ponad przednim wałem napędowym, do napędu wentylatora chłodzącego musiał zostać zaprojektowany napęd hydrauliczny. I tu robi się ciekawie, bo, zapotrzebowanie wentylatora na moc ,to przy maksymalnych obrotach silnika niemal 40kW! To znaczy, że sam tylko wentylator odpowiedzialny jest w skrajnych warunkach za odbiór ok 10% mocy wytwarzanej przez silnik. Konstrukcja wentylatora również nie pomaga, ponieważ jest przystosowany do montażu na silniku, a przez to jest solidny i ciężki, waży dobrych kilkanaście kilogramów. Ciężki wentylator w zestawie z silnikiem hydraulicznym nie nadaje się do zamontowania bezpośrednio do chłodnicy, dlatego musiałem zaprojektować dodatkową ramę, będącą nośnikiem wentylatora i wspornikiem chłodnicy, który umożliwi izolację chłodnicy od wibracji. Pomimo, że zespół chłodnica, wentylator z napędem i rama pomocnicza, zostały zaprojektowane w maksymalnie kompaktowej formie, po ich umieszczeniu w komorze silnika, zostało po 10mm luzu na stronę (było to oczywiście zgodne z założeniami projektu).

Podczas doboru silnika hydraulicznego dla napędu wentylatora, okazało się, że pompa hydrauliczna w którą wyposażony był dostarczony silnik, kompletnie nie ma szansy sprostać zadaniu do którego była przewidziana. Tutaj zabrakło doświadczenia tak mi, jak i mojemu wsparciu w firmie Deutz. Dostarczona pompa zębata została zastąpiona przystawką mocy umożliwiającą odbiór większej mocy z rozrządu silnika i odpowiednią pompą tłoczkową firmy Hydro-Leduc o stałym wydatku. Silnik wentylatora również został dobrany z oferty tego producenta. Sterowanie napędu hydraulicznego posiada w sumie 3 biegi. Jałowy, kiedy cały wydatek pompy idzie w przelew, bieg 1 dla którego możemy ustawić ograniczone ciśnienie robocze oraz bieg 2 pracujący z pełną wydajnością. Dodatkowo układ działa tak, że po zgaszeniu silnika, wentylator nie jest hamowany przez pompę i ma możliwość swobodnego hamowania. Bieg jałowy miał za zadanie nie obciążać silnika podczas rozruchu, ale w praktyce nie jest potrzebny i rozruch wentylatora na biegu nie stanowi dla silnika istotnego obciążenia. Bieg drugi również nie jest niezbędny. Projektując taki układ raz jeszcze został bym przy pojedynczym obiegu z możliwością ograniczenia ciśnienia w układzie (czyli możliwością regulacji prędkości obrotowej). Hydrauliczny napęd wentylatora chłodnicy, poza wadą w postaci komplikacji, ma tę dużą zaletę, że daje możliwość zmniejszenia obciążenia silnika pracą wentylatora lub np. daje możliwość podniesienia temperatury pracy silnika, co może być również korzystne. Na pewno jest tutaj pewne pole do szukania oszczędności w zużyciu paliwa i redukcji wielkości emisji.

Ciekawym zagadnieniem był dobór sprzęgła elastycznego, pracującego pomiędzy kołem zamachowym a przekładnią ZF. Zamówienie sprzęgła wiązało się z koniecznością dostarczenia do producenta danych związanych z wyważeniem (a raczej niewyważeniem) silnika, charakterystyką pracy przekładni ZF i podobnych w celu wykonania obliczeń. Czas oczekiwania na sprzęgło wyniósł 16tygodni, a jego koszt był astronomiczny. Finalnie zamontowaliśmy komponent dokładnie taki jak powinniśmy, wypełniając tym samym cześć z wymogów gwarancyjnych producenta silnika.
Kłopotliwym elementem instalacji okazał się układ wydechowy. Głównie ze względu na brak wyboru tłumików które byłyby dostępne na rynku z półki. Są oczywiście producenci z katalogami pełnymi produktów, ale czasy oczekiwania na poziomie 12-16 tygodni były nie do zaakceptowania. Stanęło na tym, że wykonaliśmy renowacje oryginalnych tłumików maszyny i wróciły one na swoje miejsce. Z tego elementu instalacji jestem najmniej zadowolony. Wszystko oczywiście działa jak należy, ale można było iść do przodu w kwestii wygłuszenia całego układu. Z perspektywy czasu, kwestie związane z wyciszeniem maszyny podczas takiej modernizacji, miałyby dla mnie zdecydowanie wyższy priorytet.
Integracja nowego napędu z maszyną
Sterowanie obrotami fabrycznego silnika było zrealizowane w bardzo prosty sposób. Do cięgła rzędowej pompy wtryskowej, podłączony był siłownik pneumatyczny który sterował obrotami, oraz drugi siłownik pneumatyczny, który odpowiadał za blokadę maksymalnych obrotów silnika dla trybu roboczego (podbijania) maszyny. W trybie podbijania, obroty silnika są kluczowe, ponieważ są wprost proporcjonalne do prędkości wałów agregatów podbijających, czyli odpowiadają za częstotliwość ich pracy. Sterowanie obrotami silnika musi spełniać funkcje – tryb jazdy (pełny zakres obrotów), tryb podbijania (ograniczone obroty maksymalne) oraz dawać możliwość łatwego korygowania obrotów maksymalnych dla trybu podbijania. Dodatkowo maszyna posiada 3 punkty z których operatorzy muszą mieć możliwość sterowania silnikiem (jednoczesnego, ze względów bezpieczeństwa) – dwie kabiny jazdy i jedno stanowisko podbijania. Układ z pozoru prosty, ale w praktyce zrealizowanie go z wykorzystaniem potencjometrów zamiast dotychczasowych zaworów pneumatycznych, wiązało się z koniecznością zaprojektowania dedykowanej instalacji elektrycznej i zaprogramowania conajmniej jednego mikrokontrolera. Czas gonił a znalezienie osoby, która zaprojektuje i wykona taki układ okazało się kłopotliwe. W pewnym momencie zacząłem szukać innego rozwiązania i takie rozwiązanie znalazłem, uruchomiłem i z sukcesem przetestowałem. Mianowicie, oba siłowniki pneumatyczne odpowiedzialne za sterowanie obrotami starego silnika, zastąpiłem analogowymi przetwornikami ciśnienia. Jednym pracującym w pełnym zakresie i drugim, który na wyjściu posiadał dodatkowy potencjometr, którego zadaniem było ograniczenie sygnały wyjściowego, czyli wielkości obrotów maksymalnych. Sygnały z przetworników zostały doprowadzone wprost do sterownika silnika. Nie jest to rozwiązanie idealne, ale ma jedną wielką zaletę. Dzięki niemu, obsługa maszyny przez operatorów nie zmieniła się w żaden sposób a fabryczne dźwignie sterowania gazem i przełączaniem trybu pracy maszyny pozostały na swoich miejscach.


Mam nadzieję, że opisana modernizacja jest dla Was interesującym zagadnieniem. Oczywiście, ująłem powyżej tylko kilka z bardzo wielu detali technicznych z jakimi się wiązała. Próba opisania wszystkich, sprawiłaby, że mało kto miałby dość cierpliwości, żeby dobrnąć do tego momentu. Jeżeli jesteś zainteresowany/na szerszym aspektem całego procesu to oczywiście gorąco zapraszam do kontaktu.

