Dlaczego właściwa obsługa maszyn musi z początku boleć i wykrwawiać.
W 2006-2007 roku pracowałem przez jakiś czas w Norwegii. Zajmowałem się różnymi prostymi pracami porządkowymi, wykończeniowymi, malowaniem domów i podobnymi. W tamtym czasie w Norwegii moje wynagrodzenie wynosiło 50zł do ręki za każdą godzinę. W Polsce w tamtym czasie były jeszcze prace, które „wynagradzano” stawką 5zł za godzinę (tak, pięć złotych!), a nie brakowało i artystów ,którzy potrafili przy takiej stawce oszukać pracowników i nie zapłacić im należnego wynagrodzenia. Przy stawce 10 krotnie wyższej od minimum, każda praca była lekką i przyjemną… Zderzyłem się w tamtym okresie z wieloma zjawiskami, które były dla mnie nie do pomyślenia, ale w Norwegii były już standardem.
Jedna z sytuacji zapadła mi w pamięć szczególnie i już z pewnością zostanie ze mną do końca życia zawodowego. Na jednej z robót, w trakcie mycia pędzli i wałków, Norweg dla którego pracowałem przyszedł i zrugał mnie za to co robię. Stwierdził że czas, jaki poświęcam na mycie narzędzi kosztuje go więcej niż narzędzia których używam i żebym następnym razem wziął nowe a używane wyrzucił. Dla młodego człowieka, który od początku miał wpajane, że o narzędzia trzeba dbać bardziej jak o siebie, było to nieprawdopodobne zderzenie z alternatywną rzeczywistością. Zderzenie braku kultury technicznej z ekonomią w najczystszej postaci. Teraz wiem, że był to rodzaj bardzo krótkowzrocznej ekonomii, ale faktycznie w tamtym czasie, odwrotnie niż w Norwegii, praca fachowców w Polsce była wyceniana znacznie niżej niż materiał i narzędzia, których fachowcy używali. W Polsce do logiki z którą zderzyłem się wtedy, doszliśmy dopiero kilka lat temu, a obecnie, po okresie pandemii, wchodzimy w zupełnie nowy etap rozwoju gospodarki, kiedy praca jest droga, a narzędzia potrafią być abstrakcyjnie drogie.
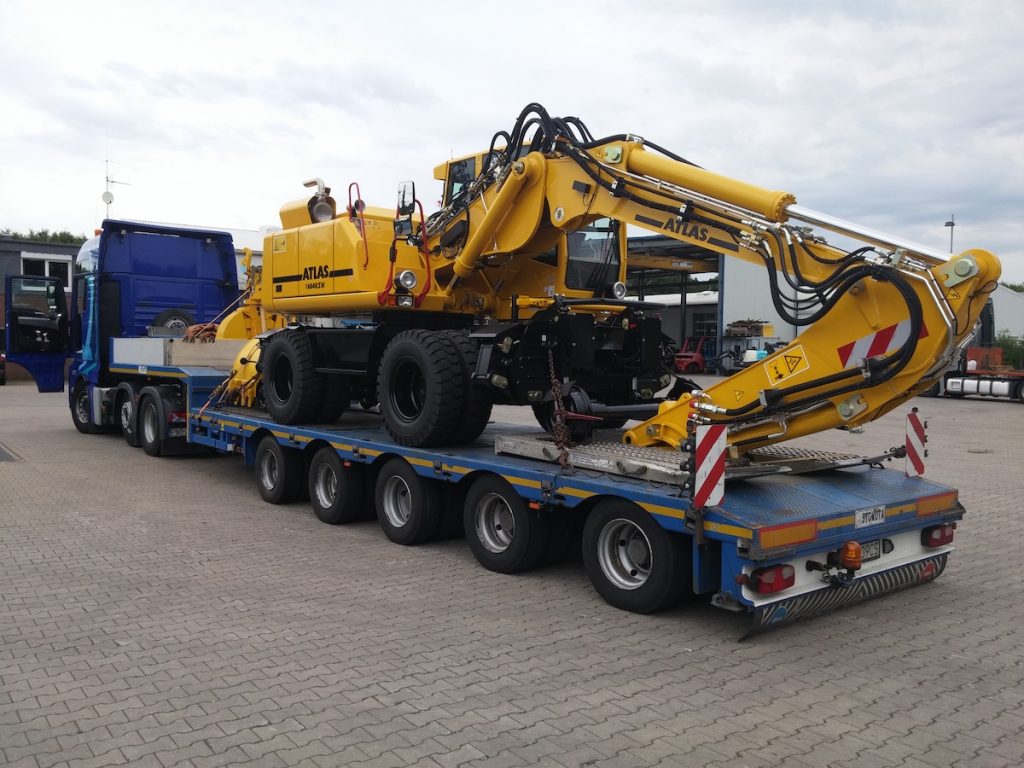
W 2015 roku koparka dwudrogowa firmy Atlas kosztowała z podstawowym osprzętem ok miliona złotych netto. W roku 2019 ok 1,4 miliona, a w roku 2024, ta sama maszyna (nie wchodząc w kosmetykę) kosztuje co najmniej 1,8 miliona złotych netto, a z dobrym wyposażeniem spokojnie możemy dojść do dwóch milionów netto. To oznacza, że zakładając resurs koparki na poziomie 20 000 motogodzin, sama stawka amortyzacji w roboczogodzinie powinna wynosić 100zł/godzinę! Czy to sprawiło, że firmy budowlane zaczęły traktować swoje maszyny jak skarby o które trzeba pieczołowicie dbać i chuchać na nie jak na kury znoszące złote jajka? Raczej nie, a powinniśmy zacząć się oswajać z myślą, że dla firmy budowlanej, każdy sprzęt, którego pracę później fakturujemy, jest ważniejszy niż cokolwiek innego, włącznie z autem, telefonem i komputerem prezesa.
Dla dzisiejszych kierowników kontraktów i robót, sprzęt jest tylko kolejnym punktem w statystyce excelowej tabelki. Działa – dobrze, nie działa – nie dobrze, i nic po środku. Nie sprzyja to kulturze technicznej i dbaniu o jego stan. Utrzymanie sprzętu jest szczególnie kłopotliwe dla firm, które nie posiadają własnego zaplecza technicznego i serwisu. Wynika to z tego, że zewnętrzne serwisy zajmują się usuwaniem usterek i ożywianiem maszyn, a nie koniecznie jego właściwą obsługą pod kątem bezawaryjności i dbaniem o dobry stan wizualny. W efekcie kupiony za ciężkie pieniądze sprzęt jest eksploatowany od awarii do awarii, a po kilku latach okazuje się, że zostajemy z brzydkim i zaniedbanym gratem, na którego wszyscy narzekają, a jego wartość i możliwość odsprzedaży mieści się na posadzce parteru dziesięcio piętrowego bloku.
Szczególnym przedstawicielem tego sposobu postępowania z maszynami, są sprzęty pojawiające się na aukcjach poleasingowych, oddane lub odebrane klientowi, w stanie wskazującym na katorżniczą pracę, a często również z defektami, których usunięcie jest już ekonomicznie nieuzasadnione. Realne okazje na takich aukcjach są naprawdę rzadkością, a jak już się pojawiają to licytacja przypomina walkę o ogień.
Jak powinna wyglądać obsługa sprzętu i dlaczego początki będą bolesne.
Do każdego uszkodzenia maszyny, które nie wynika z normalnej eksploatacji, powinniśmy podchodzić jak do realnego kosztu, który trzeba ponieść tu i teraz. Zbita lampa? 1000zł na zakup nowej, plus 200zł koszt wymiany. Wgnieciona klapa na koparce? Demontaż, naprawa, lakierowanie, spokojnie może się zebrać kilka tysięcy złotych. Zatarta zagęszczarka, dlatego że przy rozpoczęciu pracy nikt nie sprawdził czy w silniku jest olej? Kolejnych kilka tysięcy złotych, a często dodatkowo koszt zastępczej maszyny z wypożyczalni. I każde takie zdarzenie powinno być odnotowane, zaplanowane do usunięcia i raportowane po usunięciu (np. w dzienniku kosztów nadprogramowych). A osoby zaangażowane powinny mieć świadomość tego, jakie są konsekwencje i powinny widzieć, że nie pozostają bez odpowiedzi. Omawianie kosztów z jakimi wiąże się utrzymanie sprzętu, powinno być elementem dobrej kultury pracy, szczególnie, kiedy omówienie takiego zagadnienia z pracownikami, zawiera się w nie dłuższym niż 5 minutowym spotkaniu.
Z początku takie podejście może dla niektórych być przejawem histerii, ale cel takiego działania jest znacznie bardziej długofalowy, niż może się wydawać. Przede wszystkim, Wasi pracownicy z podejścia na zasadzie „stało się a za 10min już nikt o tym nie będzie pamiętał”, zaczną traktować szkody personalnie. I gwarantuję każdemu, że kolejnym razem, kiedy operator maszyny będzie planował „wpakowanie” jej w miejsce w którym nigdy nie powinna się znaleźć, zatrzyma się i pomyśli nad lepszym rozwiązaniem niż to najprostsze, ale nie koniecznie optymalne.
Kolejną konsekwencją takiej kultury obsługi będzie to, że za 10lat będziemy na placu mieli sprzęt, który nadal zarabia na siebie i firmę dobre pieniądze, stanowi wizytówkę kultury technicznej, a jeżeli zdecydujemy o jego sprzedaży, to będzie stanowił realną wartość i łakomy kąsek na rynku sprzętu używanego. Poniesione w czasie koszty eksploatacji na pewno zwrócą się z solidną nawiązką. Szczególnie dobrym poparciem tej tezy, jest systematyczny wzrost cen maszyn używanych. Zadbane 10-15 letnie maszyny są dzisiaj zdecydowanie droższe niż np. 5 lat temu, pomimo tego, że jednocześnie są 5 lat starsze.
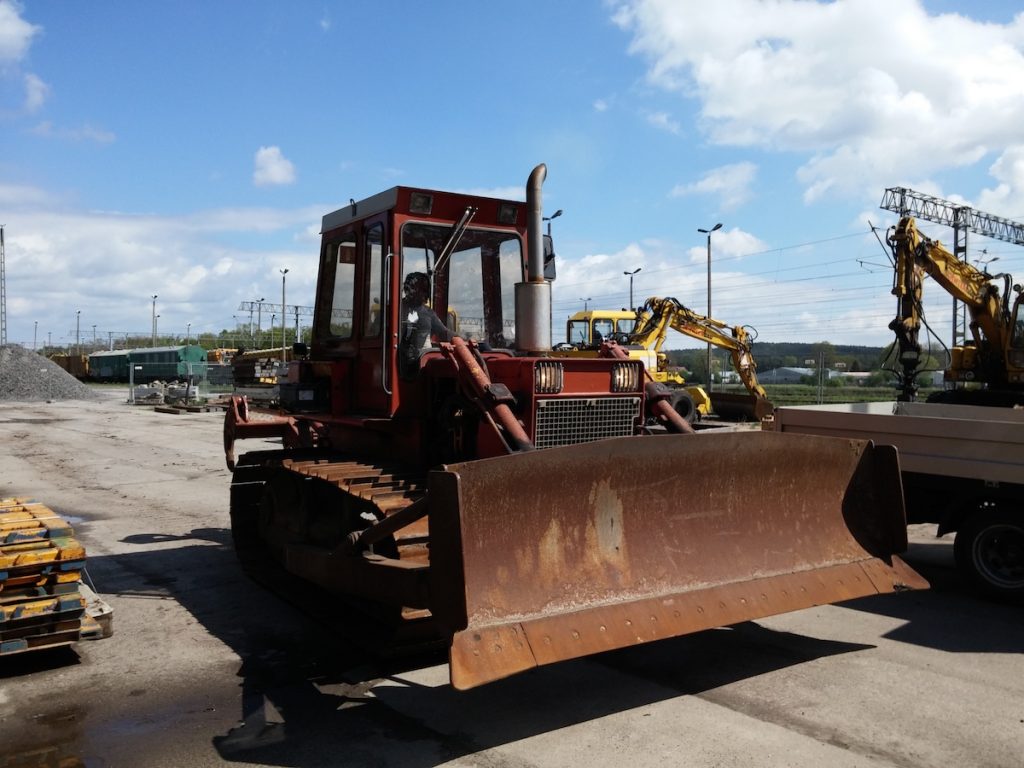
Doskonałym przykładem wysokiej kultury technicznej obsługi maszyn są rolnicy. Moi sąsiedzi mają na oko 40 letni kombajn Bizon, który nadal wygląda godnie, w większości jest w oryginalnym lakierze i sezon w sezon wykonuje pracę do której został stworzony. Jest to wynik troski jaką jest obdarzony od początku jego eksploatacji. Poza sezonem, odpoczywa pod wiatą, przed żniwami jest skrupulatnie przeglądany i przygotowany do pracy. A po żniwach czyszczony, przeglądany i konserwowany. Ktoś może stwierdzić, że niewiele pracuje, bo żniwa nie trwają długo. Powinien wtedy obejrzeć John Deere’a innego z moich sąsiadów. Ciągnik ma kilkanaście lat, jeździ w polu przez cały rok i nadal wygląda, jakby może miesiąc temu wyjechał z fabryki. Czasami zastanawiam się, czy przed każdym wyjazdem nie przechodzi detailingu w postaci polerki i nałożenia nowej warstwy ceramiki, której nie powstydził by się żaden czerwony wóz z Maranello.
Trzeba przy tym wszystkim pamiętać, że nie sztuką jest skupienie się, jedynie na karaniu pracowników za szkody na sprzęcie. Takie podejście zupełnie się nie sprawdza. Sztuką jest stworzenie systemu, w którym pracownicy są i czują się realnie doceniani za to, że dbają o mienie pracodawcy. Systemu, w którym będą mieli do dyspozycji sprzęt, którego obsługa daje satysfakcję a nie poczucia wiecznej walki z widłami i obornikiem.
Dbajcie o swoje maszyny jak o kury znoszące złote jajka, czule głaskajcie, zmieniajcie ściółkę, karmcie regularnie porządną pasza. Jeżeli jeszcze tego nie robicie, na początku będzie ciężko i drogo, ale z czasem korzyści będą piętrzyć się wysoko ponad koszty. Wasz sprzęt będzie najlepszym świadectwem profesjonalizmu dla Waszych partnerów.